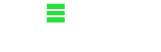
党的二十届三中全会强调,深化科技体制改革,要推动技术革命性突破,促进各类先进生产要素向发展新质生产力集聚。国家能源集团新能源研究院(以下简称“国能新能源院”)深入践行国家能源集团“1331”科技创新战略,坚定“创新是企业的责任”的理念,紧扣行业发展重大问题,依托重大工程实施重大科技创新,在以光伏发电为代表的新能源领域探索出提质增效的新路径。
向新探索 破解研发难题
我国集中式光伏项目集聚在三北地区的风光大基地,多数分布在沙漠、戈壁、荒漠地区,这些地区环境恶劣,风沙大、气温低、施工窗口期短。项目周边劳动人员紧缺,特别在部分沙漠地区,不适宜长时间户外劳动,施工周期难以把控,对风光大基地项目建设的收益率提出了更高的挑战。国能新能源院着眼于行业现实问题,力图以创新技术应用,解决风光大基地的人员缺乏和施工效率低等关键问题,以促进项目开发收益良性增长。
由国能新能源院和国电综合能源内蒙古公司、隆基绿能科技股份有限公司组成的研发团队,紧扣行业发展问题,开展“一体化组件”创新技术的攻关研究,依托鄂尔多斯采煤沉陷区300万千瓦光伏基地,开展先进技术的工程示范。目前,“一体化组件”完成调试安装,标志着国内首个针对“沙戈荒”大基地项目开发的新型组件支架示范工程取得阶段性成功。该项目形成了多个首创、首次、首台技术研究成果,关键技术研究成果达到国际领先水平,成为国内首个全天候光伏方阵机械化施工项目,国际首创光伏“一体化组件”设备及工程示范标杆。
“一体化组件”囊括了钢包边光伏组件、模块化支架、机械安装平台以及整体机械化吊装施工工艺等部分,通过多项创新技术,实现光伏电站施工建设的降本增效,提升运输效率,降低施工强度,并具有一定的抵抗不均匀沉降造成光伏组件和支架破坏的能力。整个项目全过程均为自主研发,技术可控,拥有自主知识产权,且全产业链国产化,具备大规模推广应用的可复制性。
催生新模式 提质增效续引擎
通常,光伏组件和固定支架的安装效率为1.18人×日/组串,“一体化组件”创新解决方案采用机械化安装平台,安装效率为0.85人×日/组串,相比常规方案生产效率提升28%。按照一个班组5人估算,每天工作8小时,常规方案日产量为60.6千瓦,而机械化模块施工,日产量高达84.1千瓦。
大型地面电站通常采用的光伏组件为铝合金边框,即通过4个螺栓将组件与独立2×13布置的钢支架进行连接。而“一体化组件”采用C型钢包边,组件和支架间不需要螺栓,以插入式连接,支架主要构件采用无螺栓承插式节点,将组件和2×6或2×7小单元支架视为一个整体模块。承插式的模块拼装,极大程度地简化了结构件和工序。
同时,轻量化的模块安装,通过安装平台和吊装机械完成施工,大幅降低了安装人员的劳动强度。在光伏电站施工过程中,首先进行机械安装平台的现场搭建,即由2名技术人员和6名施工人员用时3天完成4条机械化生产线的搭建和调试。4条机械安装平台生产线同时开工,在50人×日和4台机械台班情况下,每天可完成1兆瓦峰值钢包边光伏组件和模块化支架的拼装和吊装施工,整体施工效率提升20%。
“一体化组件”解决方案从概念提出,到研发验证,再到大规模应用,历经磨难,在低质内卷的光伏市场寻得“破题思路”。在光伏电站中,使用自动化机械安装平台,将工业产线搬入光伏电站,提高机械化、少人化、智能化施工占比;首创钢包边光伏组件,并采用光伏组件四边无螺栓紧固,进而实现大规模应用;首次将2×13(一个光伏组串)划分为2×7和2×6两个固定模块单元,模块单元间相互独立,减少不均匀沉降对支架和组件造成的破坏,并减少桩基础的数量和施工量;首次在支架上使用模块支架和承插式连接节点,减少螺栓的使用,提高安装效率;首次大规模采用组件支架吊装施工,创新多种专用工器具和施工工艺,进一步提高机械化施工占比和施工效率。
(作者:乔加飞,系国家能源集团新能源技术研究院设计优化研究中心主任)
第2届光伏智慧运维及人工智能大会暨储能运维大会